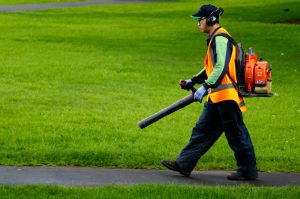
1. Commitment
The first step is commitment. Commit to a safety program that works. Make it an expectation that is upheld and keep your team accountable.
You want your employees to respond well to the training. Simply nagging them with long meetings will not keep them on their toes. In addition, crew leaders are most likely not trained in adult education. Meaning, they will not teach the importance of safety in a manner that employees with uphold.
Employees will respond to hands-on-training, just like with everything else. So, treat this as a time to get them excited about new equipment. Bring in all the safety gear and have them try it on. This will demonstrate how it is used and effective.
For larger companies you may be able to hire a designated safety person to monitor the crew. Most likely though, assign this responsibility to the crew leader. Properly educate the leader on how to enforce the safety protocol and keep the crew accountable. Some companies even use a reward system to encourage and reward safety measures. Implementing bonuses, gift cards or simply giving recognition can go a long way.
These measures should be explained in detail in the employee handbook and taught to every new employee. Make sure you and your crew leaders are setting a good example for the team. If you aren’t following through with protocol they will assume they don’t have to either.
2. Awareness
Next is awareness. Depending on your area, additional safety training may be required. For instance, your team may need to take extra precautions using a type of equipment that isn’t used in other areas. Or you may need to educate your team on laws and regulations that differ in one area to the next.
Be sure that specialized training is happening on a continual basis. Going over safety just once a week for 10 or 15 minutes can make a big impact. Bring in the equipment and make your team aware of the risk they take when not following protocol. Although, being strict on safety is important, make sure employees feel comfortable reporting slips. As a n owner, knowing about instances that nearly become a safety concern will help you to better implement a safety strategy. For instance, teaching employees to report glitches in equipment before they completely fail can save time and a possible safety risk.
3. Response
4. Training
As mentioned, training is very important. Using videos, hands-on-examples and taking courses are all good training sources. Don’t just pick any training video or course. Make sure you thoroughly evaluate any training materials so that they accurately reflect what your employees need to do. There is no benefit is making them watch a video or attend a class that isn’t applicable to them.
Also, document your training! Keep track of what training each employee receives. You want to make sure everyone is receiving the appropriate training and that they sign verifying they took the class.
5. Evaluation
After all is said and done, it’s important to take a hard, honest look at the training you are delivering. For one reason or another, a safety concern will arise at some point in your company. It is better to be prepared and have properly trained employees that can handle the situation rather than make it worse. Consider implementing a safety program that is appropriate for the services you offer.
If you already have a plan in place. Take time to review it continually as things naturally change within an organization. You want to make sure your operations are being run as smooth and efficient as possible.



